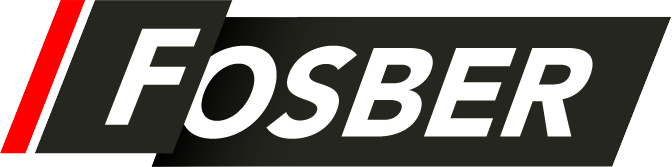

COMPLETE CORRUGATOR

STAND & SPLICER - LINK & STAND M2
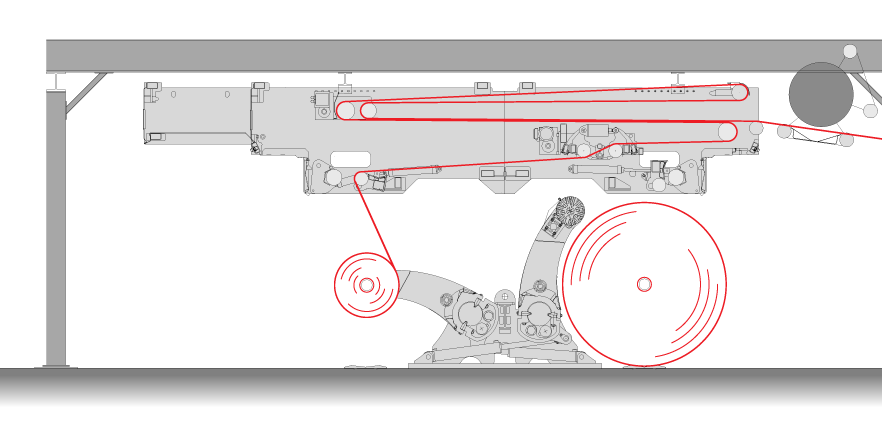
- Intro
- Gallery
The Link automatic splicer provides the latest automatic splicing technology, integrating precision and reliability through simplistic design. It can be associated with our rollstand model Stand M2, available with manual or semiautomatic roll loading system.
The Link essentially consists of two splice preparation units, two splice heads, an accelerator roll and a festoon management area. The two fixed splice preparation units are conveniently located at each end of the machine position providing simple, quick and safe splice preparation for the operator. Each splice preparation unit consists of an alignment roller, a support bar for the splice preparation, and a contact bar that serves to hold the paper firmly in place while the operator applies the double-sided splicing tape without the need for vacuum preparation bars.
Once the splice tape has been prepared the operator simply initiates the machine to go into splice position via the push button console. The system automatically positions the prepared paper into exactly the correct position ready for the splice cycle, eliminating any possibility of operator error due to improper indexing. Fixed splice head positions ensure automatic tail-grabbing is accurate and reliable.
A motorised mobile carriage houses the two splicing heads which consist of the cutting knife, the upper nip splicing roller and brake. The carriage automatically aligns the correct splice head into position according to which of the two splice stations is to be used. To initiate the splice sequence the brake automatically drops down to hold and stop the expiring paper. Then in a single action, actuated by a solitary pneumatic cylinder, the blade cuts the expiring paper while a high pressure rotating nip is created to ensure true adhesion of the two papers. The simultaneous action bonds the leading edge of the new paper to the expiring tail, accurately completing the splice within 0.25s. No impact nor hammer type mechanisms are required. The result is a true zero tail splice at maximum line speeds.
An AC driven accelerator roll is located at the paper exit end of the machine to improve overall pulling control as well as facilitating paper thread up. It serves to rapidly and securely brake the web on the old roll and to accelerate the web from the new roll back to line speed. The accelerator roll works in perfect equilibrium with the splicer's servo controlled double-roll dancer assembly to automatically monitor and maintain constant web tension at all times throughout the splice sequence. A precise amount of festoon is created during the splice cycle to provide the correct web tension according to actual paper running speed. The Link is fitted as standard with touch-screen with on-screen diagnostics and maintenance procedure controls. The machine is equipped with an array of guarding and E-stop devices to ensure safe operation.
INTEGRATED STAND & SPLICER - LINK M3
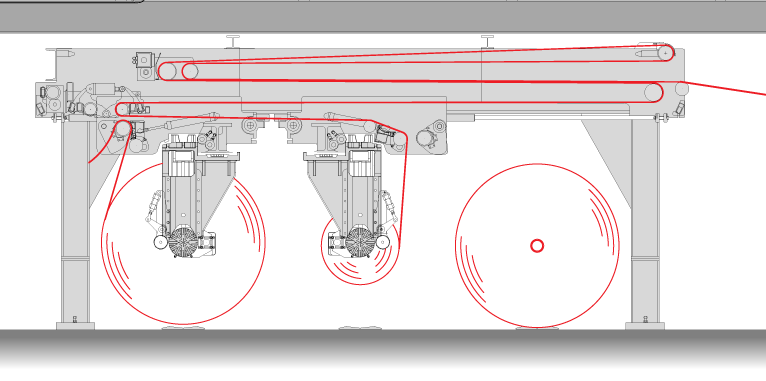
- Intro
- Gallery
The Link M3 combined roll stand & splicer group is a unique integrated solution for the optimum running of paper rolls on the corrugator, providing the shortest continuous automatic roll change cycle time available in the industry. Even if the corrugator is located close to a wall, as all reel handling is contained to just one side of the corrugator the Link M3 roll change cycle time (70% less than conventional systems) is completely unaffected.
The Link M3 is a stand-alone machine, housed in a robust modular structure which also acts as the bridge support. The reel stand section sports all the latest technical features for the automatic centering and alignment of the rolls prior to loading on the chuck arms. The independent chuck arms automatically pick up the rolls and allow automatic web alignment. The arms are fitted with an automatic core ejector as well the latest multi-disc brakes which ensure even controlled tension over time. Furthermore the arms are also fitted with automatic reminders so that after splice out rolls are automatically rewound and ejected from the Link M3 area. This means once the operator has prepared the splice he can vacate the area and carry out other duties, thus reducing overall manpower requirements on the wet-end.
The state-of-the-art splicer section of the Link M3 comprises an accelerator roll to rapidly and securely brake the web on the old roll and to accelerate the web from the new roll back to line speed. The accelerator roll works in conjunction with the servo controlled double dancer roll assembly in a perfect equilibrium for optimum and constant tension control.
The Link M3’s patented splice head design uses a single continuous movement to carry out the splice via a rotating nip to secure the splice with no impact or hammer mechanisms required. The result is a true zero tail splice at maximum line speeds with unparalleled splice reliability.
COMPACT STAND & SPLICER - PAPERLINK
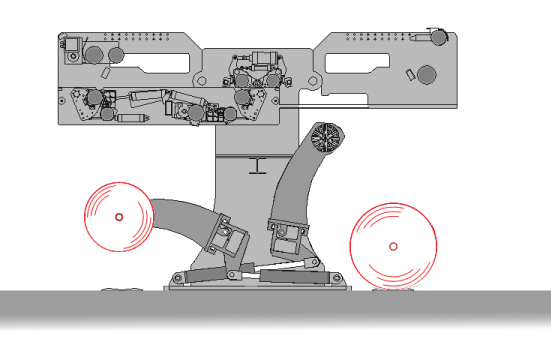
- Intro
- Gallery
The Paperlink is a compact integrated splicer roll stand machine unit. It comes in versions for 250mpm splice speed (4m long) or 300mpm splice speed with the extended festoon (5m long). This integrated design has reduced Paperlink's footprint not only in machine direction but also allows compatibility with much lower bridge heights. In addition this design also reduces PaperLink’s installation time and freight costs.
The Paperlink has a fixed upper splice head positioned in the centre of the machine and a mobile lower splice head carriage which moves to the two outer sides of the machine for easy splice preparation when called by the operator. The patented splice sequence is all carried out in a single continuous movement.
The roll stands are able to handle 3.7T paper reels or 4.2T jumbo reels with the double hydraulic cylinder option.
Other options include the Automation Pack for auto core location and automatic reel loading and unloading complete with integrated core ejectors. The TAIL LINK option involves the installation of photoeyes on all four chuck arms to automatically detect and initiate end of reel splicing or to automatically carry out a splice if a paper break has occurred.
When required for a stand-alone installation the PaperLink can be equipped with its own independent electrical cabinet and touchscreen control panel.
SINGLE FACER - SMART
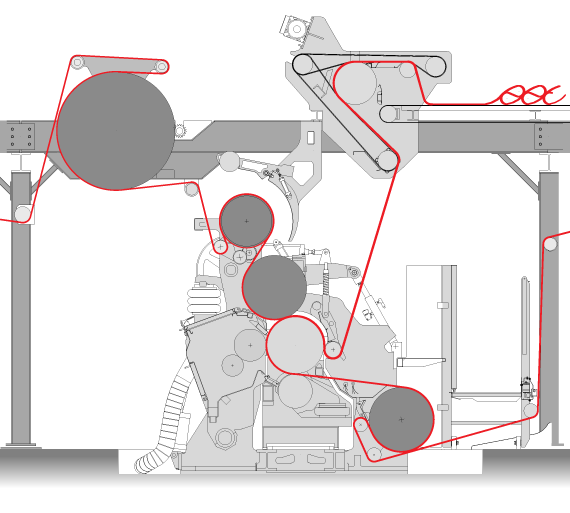
- Intro
- Gallery
The Smart single facer is a high speed, quick flute change, cassette machine, housed in a very heavy duty, rigid cast iron frame. The massive, low-vibration construction, and low center of gravity ensure the smoothest running on all flute types. The finely adjustable pressure roll is vertically off-set from the corrugating rolls to further reduce vibrations.
Roll change is accomplished through either side of the machine in as little as 10 minutes utilizing a motorized cart. All hydraulics have been eliminated from the single facer and have been engineered into the cart, resulting in a simple, reliable machine.
The differential design of the corrugating rolls greatly reduces the flute forming labyrinth, dramatically reducing paper tension and allowing optimum flute formation. The corrugating rolls are peripherally heated for virtually instantaneous heating across the surface, preventing condensate problems, and eliminating the need for siphon pipes (The live steam is cascaded first through the upper corrugating roll then to the lower corrugating roll, followed by its flow into the pre-conditioner roll where the condensate is removed). The corrugating rolls are supplied either in chrome or tungsten coated according to customer preference and flute type.
Perfect bond is maintained via the beltless extended nip system which provides a very large wrap around the upper, larger diameter corrugating roll. In addition, positive pressure holds the medium to the upper corrugating roll, providing optimal heat transfer into the medium. The pressure roll gap is automatically adjusted for various board grades and production speeds. The result is maximum production flexibility allowing all grades of paper, from lightest to the heaviest to be run simply and effectively via the automatic engagement of the pressure roll. This concept virtually eliminates pressure lines.
The Smart design incorporates a perfectly aligned 90-degree angle between the applicator roll and the flute tips. The unit continuously monitors this process, assuring the precise quantity of adhesive is applied to the flute tips.
High speed glue dam control guarantees adhesive is applied precisely to the outer edges of the medium. For cleaning and maintenance the entire glue unit is pivoted away from the main unit at the push of a button, where an automatic wash-up cycle is initiated.
GLUE MACHINE - MPH & CREST
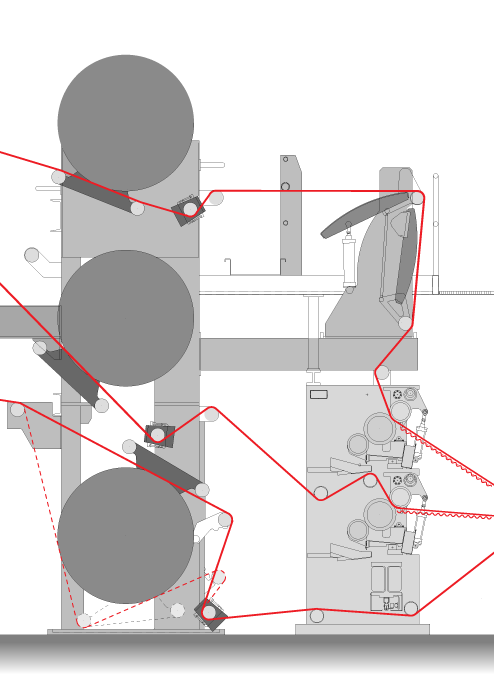
- Intro
- Gallery
The Crest glueunit compact design meets maximum production speeds and is capable of running the full range of board grades and flute types.
Eccentric flanges, fitted on both sides of the machine, provide parallel adjustment of the doctor roll to the applicator roll. The gap between the chromed doctor roll and the applicator roll is controlled to an accuracy of 0.03mm, achieved via a high precision servo gearbox. The Anilox glue applicator roll (300 mm. diameter) and the doctor roll have the same drive.
The glue gap can be run either manually (the operator sets target gaps and the machine automatically maintains such a gap), or fully automatically (the gap is set according to the pre-configured glue curve), where a constant glue film thickness is ensured at all speeds.
The Crest is supplied with a contact bar or a rider roll system, according to customer requirements. The rider roll configuration is attached to an upper arm that pivots. This can be adjusted through a finite control altering the position through a zero backlash jackscrew. This design provides absolute gap accuracy and adjustment, guaranteeing the starch is precisely applied to the flute tips only.
An adjustable width stainless steel glue pan is specifically designed to prevent glue slinging. Each operating level and its corresponding starch flow control are fully independent from the other level, allowing accurate glue film application at all speeds. Starch is fed into the center and drains out through the full lenght of the pan.
The glue reservoir is automatically kept at constant levels. The glue film is always under constant hydrostatic pressure, allowing accurate glue film application at any speed, in addition to reducing starch consumption. To facilitate cleaning, the entire glue pan can be tilted away.
The on-board drive panels and operator console is standard with touch-screen control, providing visualisation of data, machine settings, alarms, comprehensive machine diagnostics and manual over-ride.
DOUBLE FACER - EXPRESS

- Intro
- Gallery
Utilising the most up-to-date technology available today the Express double facer is capable of running the full range of board grades up to a maximum paper width of 2800 mm. Gradual and efficient heat transfer is precisely managed and controlled to achieve and complete an optimum bond whilst maintaining an equal moisture balance according to the running speed and particular board grade being produced.
The Express double facer consists of a heating section, subdivided into two or three independent stations with the option of an additional independent "zero section" right at machine infeed as well as an AC driven traction section. At the inlet of the machine, the Express is fitted with a standard curved hot plate to preheat the bottom liner or with a 500mm diameter preheater drum with variable motorised wrap arm control.
The main heating section is composed of a series extra large heavy-duty spheroid cast iron hotplates each 750 mm long in machine direction to prevent heat deformation. Thanks to its fully modular design the overall length of the heating section is fully flexible from a 9 to a 20 hotplate machine configuration depending on each customer's individual production needs.
The cast iron hotplates are manufactured using a single casting and provide much superior thermal stability when compared to steel and result in a very durable, uniform, and low-frictional surface contact with the board over a much longer life. The hotplates are formed with an internal serpentine loop specifically designed to provide a continuous, high volume fluid steam flow inside the chest. This process ensures a very efficient heat transfer whilst removing condensate, which is then fully recovered via the on-board steam system design. Each independent steam section can run from 15 bar down to 0.5 bar. The result is a perfect and uniform heat distribution to the surface of the board.
To exert a constant and even dispersion of pressure on the web the Express utilises a series of specially designed full-width yet semi-rigid shoes attached via a spring steel design to an upper moveable I beam support structure. In this way pressure is perfectly equalised at both ends of the shoes right across the full width of the web thus preventing spiking. Downward force of the shoes is exerted by variable controlled hydraulic cylinders fitted at the ends of each separate shoe section.
The outer I beam shoe support bars can be individually raised via pneumatic actuators and at the same time the whole shoe support frame structure can move laterally with respect to the centre line so pressure can be lifted off the belt right at the point of the board edge. This prevents edge crush and prolongs belt life.
The machine program allows the shoe pressures to be set either constantly or gradually (from high to low or vice versa) in board direction according to line speed and type of quality being run. Thanks to independent heating and pressure sections with separate controls, maximum flexibility is provided in terms of the automatic setting of shoe and steam pressures according to the board quality being run. The on-board touch screen control allows operators to control and set all double facer functions and processes within its database as recipes for the various qualities run. It also displays diagnostics, machine status and maintenance operations.
Similar to the heating section the traction section consist of a series of unheated plates below the web and a set of spring loaded full width pressure shoes from above to exert an adjustable and uniform pressure on to the board over a large contact area to optimise board quality.
The head pulley section is fitted with a more energy efficient AC drive system sized and configured to individual performance requirements as either a single or a double AC motor arrangement. Both upper and lower belts are fitted with an automatic tracking and alignment system as well as a heavy duty self-tensioning device to eliminate slack and further prolong belt life as well as enhance board quality.
ROTARY SHEAR - ROTARY SHEAR CS
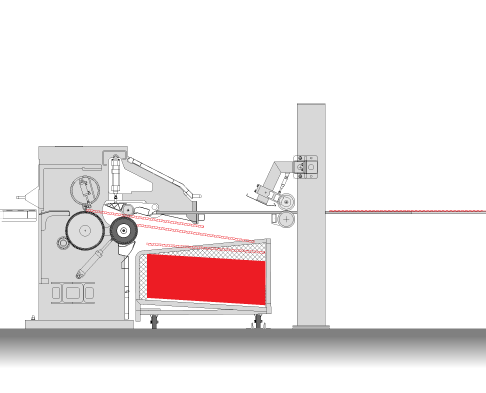
- Intro
- Gallery
Fosber's patented CONSTANT SYSTEM order change allows a true gapless order change on two knife levels through the cut-off knife. The problems of conventional order changes are eliminated by removing the need to sever the web at the rotary shear. This unique order change sequence requires the installation of the CONSTANT SYSTEM Rotary Shear with the Fosber TWIN automatic slitter scorer.
The CONSTANT SYSTEM Rotary Shear operates as a standard blade to soft anvil rotary shear in all respects except that the knife shaft has a series of 26 segmented blades which can be independently activated into cut mode. The lower anvil shaft is covered with sectioned polyurethane sleeves with a male to female locking design, for easy removal and replacement. The waste expulsion section is identical to a standard rotary shear, consisting of a pneumatically indexed diverter plate, an expulsion nip roll and a high-grip expulsion belt as well as an upper no-crush roller which applies positive pressure on the board at waste discharge.
The CONSTANT SYSTEM Rotary shear can operate as a conventional shear, chopping out waste or making a full width single cut to initiate a conventional order change, as well as gapless order change mode. In CONSTANT SYSTEM order change mode, individual blades are engaged to cut selected areas across the web. At order change, the required blades are indexed and the knife bar makes a single turn, cutting the web at only the side trim locations and the central area between the upper knife and lower knife web-divided points for the old and new order. When the order change area of the web reaches the Fosber TWIN slitter, the trim and dividing slitting heads are activated to create an overlap of the old order and new order divide slits while all other scores and slit heads are lifted out of the board line.
Fosber's CONSTANT SYSTEM Order change simply and effectively unifies the old and new orders so that a continuous flow of board runs through the web at all times – including order change. This eliminates problems associated with other order change methods such as: Reduced speed for order change, High acceleration of the old order, Jam ups due to leading edge at the slitter or knife, web weave, sheet variation at order change, and switching of measuring devices. The risk of Jam-ups is eliminated.
SLITTER SCORER - TWIN
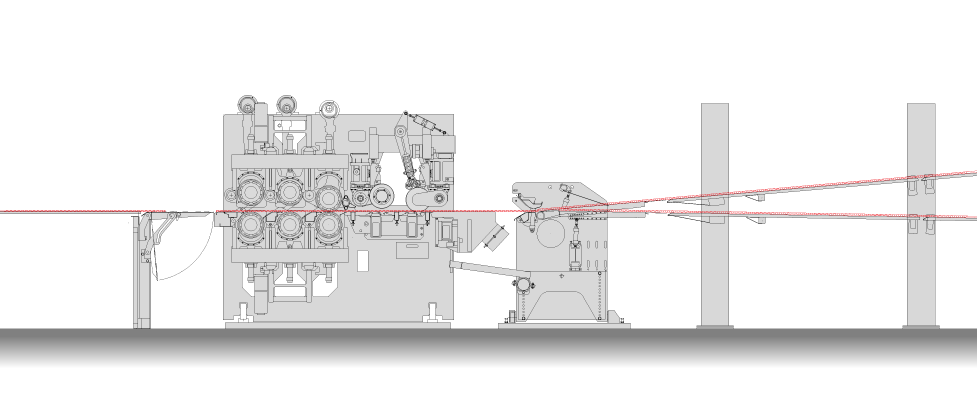
- Intro
- Gallery
Fosber's latest slitter scorer model Twin is a compact, low-maintenance machine. Two independent slitting stations and two independent stations groups allow the Twin to instantaneously order change both in GAPLESS or GAP mode without any kind of speed limitations. Precise and fast positioning of the tools for the next order is accomplished via three independent robots, which move along a rack system guaranteeing performance, reliability and accuracy.
The Twin is equipped with thin-blade Kleen Cut slitting as standard. Customers may chose whether the machine is configured with slitting from below or above the board-line as they prefer.
The utilisation of tungsten carbide blades guarantee a superior slit quality without the need for blade lubrication, thus providing the Twin with a perfect slit profile for all types of paper and board combinations.
The automatic blade sharpening system is common to both slitting stations and consists of a double grinding head assembly mounted on the slitter robot.
Extremely low maintenance costs are obtained thanks to the development of a completely new and innovative counter blade system. The blades cut against a fixed steel anvil which holds a segmented Teflon bar. Maintenance is virtually eliminated as the segmented Teflon strips are not only self-loading but are periodically re-indexed via an automatically controlled displacement system.
The two scoring stations are identical and can be equipped with different score profiles thus enhancing the production versatility of the Twin. This also allows the running of different score profiles simultaneously when run in tandem mode - even when an auxiliary score shaft is not present.
Each slit station can be fitted with a maximum of 9 blades for running 8 boxes out. If more than 8 boxes out are required, the slit stations would similarly be automatically managed to run in tandem mode so that both slitting stations would be engaged at the same time. This is also made possible as each blade can be individually engaged or disengaged from the board line. This feature allows quick and simple blade replacement (2 minutes), optimised and evenly spread usage of blades right across the web, and the ability to simply exclude an individual blade if necessary without stopping the machine. The high speed robotic set up system utilises a brushless AC motor directly keyed into an epicycloid planetary precision gearbox. This in conjunction with the rack system (along which the robots move) mean that very high and precise positioning speeds are obtained.
This greatly reduces set times and permits the running of the shortest possible orders. Furthermore after each set-up the slitter robot carries out a fast scan of all the slitting blades and its unique sensor system verifies that all tools for the next job have been correctly positioned, thus providing even greater machine protection and reliability.
CUT OFF KNIFE - MASTER

- Intro
- Gallery
The Master cut-off knife is comprised of three main sections – the infeed delivery section, the cutting section, and the outfeed delivery section.
The intelligent design of the Master cut-off knife allows for short sheets to be run at the industries highest line speeds. The outfeed delivery section consists of an independently driven no crush exit roll and vacuum belts. The outfeed system can also be fitted with a sheet diverter system on each knife level to automatically eject order change sheets and all splices, while constantly maintaining a continuous unbroken flow of web through the dry-end at all times and at full line speeds.
The waste divert system will also eject out-of-register preprint sheets and any waste board that has been automatically detected by Fosber’s Pro/Quality defect detection system, ensuring that only 100% saleable sheets are delivered on to the downstacker. The ejected waste sheets at each level are diverted on to a waste conveyor and laterally discharged to either the operator side or drive (or both sides).
This means quality checks of the sheets can be very easily and safely carried out here at any time, significantly reducing the manpower requirement and workload on the stacker and catwalks. The waste diverter system has a cassette design allowing it to be completely extracted from the machine for much easier maintenance.
The Master cut-off knife can also be fitted with a self-positioning “digital ready” automatic cut-to-pattern recognition system for the running of pre-printed liners. The system automatically and instantly synchronises on the target mark and can be configured to run pre-printed on both the top and bottom sides of the board. Preprint orders can be run fully automatically on a back-to-back basis, with different preprint orders being run simultaneously on each knife level with practically zero waste and without the need for any operator intervention whatsoever.
In order to meet different production requirements the Master is available in various performance levels, corresponding to the number of drive control units. All drive motors are brushless AC motors and cut length precision is guaranteed via a Vector Drive Control with a power recovery system, greatly reducing power consumption. The Master cut-off knife is run by a high performance control system featuring: Order visualization, Machine Status, production Data, Fault Diagnosis, and Operator override facilities.
The system also allows the Master to communicate with other dry-end machinery and scheduling systems, as well as enabling remote access via modem or network connection for additional Fosber diagnostic and support services. Operator safety on the Master Cut-off knife by use of extensive guarding and lockout devices will satisfy the most stringent of company or government standards.
STACKER - TERMINAL
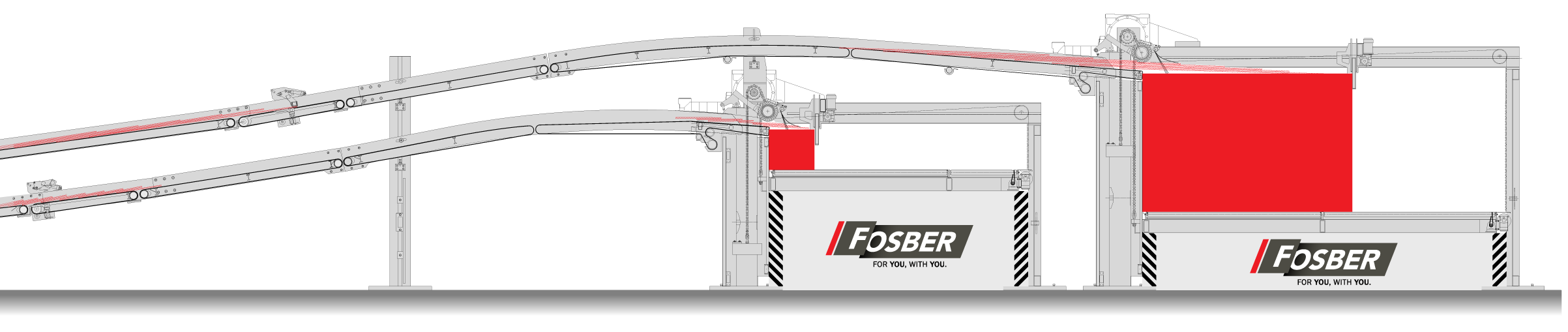
- Intro
- Gallery
Fosber's latest automatic stacker system, the Terminal, can be configured with one, two or three independent stacker levels. Essentially the Terminal is composed of independently controlled conveyor belt sections, a braking section, a separation section and a downstacker type elevator deck expulsion section.
From the cut-off knife sheets are delivered on to the Terminal where they are first shingled and aligned on the braking section via a guided vacuum belt and an automatically controlled brush group assembly. The control system, according to a personalised pressure curve set at each individual installation, dynamically adjusts the variable pressure on each of the five brushes according to the sheet width, sheet length, the flute type, and actual running line speed being run. The combination of the vacuum belt and the brush assembly guarantees optimum stack quality right from the moment sheets are fed in to the Terminal.
Stack changes are accomplished via a moving clamp system which ensures clean and precise stack separation as well as allowing the fastest possible expulsion cycle times. The result is that stack/order changes can be carried out at the highest line speeds, while continuously maintaining the best stack quality available in the market.
Precision control of the elevator deck also assists in making sure optimum stack presentation is achieved at the highest machine speeds - whatever the type and size of product being run. This is thanks also to the introduction of an innovative new system whereby the angle of in-feed of the last belt section into the elevator deck is automatically adjustable according to the sheet size and flute type being run.
The stacker deck is fitted with a full width belt over roller section to provide greater stack stability and ease of expulsion. This means even the most difficult sheet sizes can be discharged without compromising machine performance nor operator safety. As an open and accessible machine the safety mechanisms (such as a double security chain, anti-intrusion laser scanners etc.) have been carefully implemented to provide unparallel safety levels on the Terminal. The result is that the machine completely supersedes all the requirements laid out in EN 1010-5:2005, the industry's standard European CE Safety Directive.
The Terminal, thanks to its stand-alone intelligent machine program is able to continuously and dynamically adapt to exactly the type of production being run. The result is precise stack quality, at the highest speeds, under all production conditions.
SUPERVISOR - Pro/Syncro

- Intro
- Gallery
Fosber's corrugator is controlled by the Pro/Syncro supervisor system. Pro/Syncro can be supplied either as a pure wet-end control system, a pure dry-end control system or a total corrugator control system. Automatic wet-end features of Pro/Syncro include bridge management and calibration, synchronisation of speed and splices, partial reel label printing, roll stock management interface, roll stand monitoring, paper break detection, wet end order change as well as full displays for machine status, alarms and diagnostics. Fosber's Pro/Syncro dry-end control supervisor provides detailed production reporting, intelligent diagnostics, pallet label print-outs, and data links to the wet-end, office and scheduling networks, and materials handling control systems. Pro/Syncro can even be further expanded to offer a fully automatic process control system.
Physically, the Pro/Syncro control system is comprised of a control panel, positioned adjacent to the other dry-end machine control panels, thus offering easy access to the operator. A certain number of client PCs with cubicle displays can be added to the main Pro/Syncro server PC Ethernet network so they can be located in any preferred area on the corrugator line. This allows the corrugator to be controlled and managed also from areas outside of the control room.
The Pro/Syncro architecture is designed with two separate networks on which all the necessary devices are connected. One network is dedicated to all the devices that enable Pro/Syncro to synchronise all the machines on the line and to monitor production progress in Real Time. The other network is for data exchange purposes that allow Pro/Syncro to interface to the various control systems present on the line such as machine/office/printer supervision controls) etc. The standard Pro/Syncro architecture can be expanded to meet the customer's requirements and to assist in facilitating various operator tasks.
Pro/Active
Pro/Active is an closed-loop control system that automatically monitors and controls all the various settings and variables of the corrugating process, reducing waste by ensuring a proper bond and optimum quality flat board is produced.
This is achieved by measuring and monitoring temperatures and moisture levels at strategic positions long the corrugator line, and then automatically adapting the various machine and system parameters to ensure that the ideal target process settings that have been set and personalised for each individual board type quality the plant produces are met.
The Pro/Active will therefore continuously automatically set and adjust all such settings such as the variable wrap arm positions, steam pressures along the corrugator, steam showers, all glue gaps, double backer steam shoe pressure settings as well as the paper tensions in the splicers and at the bridge brake. The closed-loop control system also allows instant automatic correction of any warp detected (either by the operator or by automatically by a laser bank) in either machine or cross-machine direction system.
The simple and intuitive main operator interface page not only shows all the operator all the current settings but also allows the operator to quickly fine tune and adjust the settings for any individual quality type being run, which can then be easily saved to the database if desired.
The “Record” feature is a further enhancement to the Pro/Control and an extremely useful tool that collects & stores (for up to 12 months) all the historical production & process data for every single dry-end order run off the corrugator. This feature records, stores & generates graphs of all relevant data such as actual running speeds, the specific IDs of each individual paper reel actually used to run that order, as well as all the main corrugator process settings such as the steam pressures, wrap arm positions, temperature and moisture readings, starch dosages, shoe settings etc. so target settings can continuously be monitored, checked and optimised. Furthermore Record provides our customers, as well as their own subsequent customers, with a complete “provenance” of every individual packaging order produced on the dry-end over the last 12 months.
The flexibility and range of features within Pro/Syncro provide an extremely powerful toolbox that adds significantly to corrugator productivity and quality of product and standardises how corrugated board is produced across different plants within the same group. At the same time results in lower costs thanks to a reduction of waste and far fewer claims as well as less starch and steam consumption.
ENHANCED CONTROLS

- Intro
- Gallery
Introducing its latest performance enhancing software system, Fosber launches Pro/Care and Pro/Quality for its latest generation corrugators.
As the corrugated industry begins its journey into ‘Industry 4.0’, equipment manufacturers are looking at ways to future proof machinery designs. With the emphasis on designing intelligent machinery, manufacturers are now focussing their attention on software systems that will help ensure maximum uptime and minimum disruption to daily routines and enhanced quality of corrugated board.
With its latest generation of Smart corrugator, Fosber has now launched Pro/Care and Pro/Quality, an online system for real time monitoring and recording of all data on the corrugator, as well as defect detection, correction and ejection.
Pro/Care
The core concept of Pro/Care is to remove the total reliance of this vital aspect of maintenance of the corrugator on people, by having the machine itself dictate exactly which services are needed to be carried out.
By continuously capturing actual production, process and machinery data in real time, Pro/Care is able to intelligently and scientifically manage the maintenance and technical support, as well as providing pre-emptive diagnostics and unprecedented data analysis. Based on the actual captured production data and usage of the corrugator, Pro/Care identifies, plans and instructs which pending maintenance tasks need to be carried out and when.
Pro/Care details exactly which resources, man hours, equipment and parts are required to carry out the scheduled maintenance. It illustrates the relevant step-by-step procedures through easy-to-follow video and photographic instructions and generates both maintenance reports and proposals for new and future activities.
The interactive search facilities allow users to instantly locate and browse the maintenance procedures even when they are physically working inside the machine thanks to convenient accessibility via tablets or smart phones on the Pro/Care WiFi network. This feature of Pro/Care was developed not only as a valuable on-line intelligent maintenance system, but also as a training tool to allow operators to continuously enhance their knowledge of the corrugator, thanks to its interactive features.
Pro/Care’s enhanced analytical software suite provides continuous productivity and process recording and reporting thanks to its full interface and integration to Fosber’s Pro/Syncro corrugator control system. Flexible filters and abstract reporting features provide detailed analysis across any desired input period over the last 12 months – whether by flute, board quality, machine, process parameter, downtime, shift, order, format, paperweight, speeds and so on.
Two additional modules of Pro/Care continuously monitor and record important consumption data for both diagnostic and analytical purposes. The CMD (Corrugator Machine Diagnostics) module constantly monitors all the main motors and their associated kinematic chains, simultaneously cross referencing this data with the actual running conditions and type of production on the corrugator. The system establishes a self-learning correlation matrix between the measured current consumption of all the kinematic chains against the actual parameters of the running corrugator. In this way, it provides real time diagnostic analysis as it is able to instantly identify any anomalies that arise outside the predicted tolerance absorption bands. This results in Pro/Care automatically notifying and activating the Fosber customer care department, allowing potential issues to be indentified and addressed though pre-emptive measures before they become actual problems. CMD has already proven itself to be a powerful tool in the first field installations. Similarly, the CCM (Corrugator Consumption Monitoring) module measures actual steam, electrical power, compressed air and starch consumption during operation of the corrugator, which is cross referenced in real time with the type of board production currently running. These values are recorded and stored in Pro/Care and are useful, not only for further machine diagnostics but allowing post-evaluation for a complete analysis of cost optimisation, energy usage and overall sustainability.
Thanks to scientific and intelligent on-line maintenance programming, real time monitoring and recording, enhanced data analysis and pre-emptive diagnostics, Pro/Care can assist in maximising the uptime and overall corrugator efficiency.
Pro/Quality
Pro/Quality is a defect detection and monitoring system that is installed at each single facer to monitor the web immediately, at source, as it exits the machine just prior to the take-up conveyor. Utilising vision techniques and technologies, Pro/Quality monitors, detects and records in real-time any defects across the full web width with 100 per cent coverage.
It detects all web surface defects such as paper defects, as well as any 3D defects such as delamination, bubbles, blistering, folds, wrinkles, tears, splice joints, flute crush or edge defects. The system is intrinsically linked to Fosber’s Pro/Syncro corrugator control and wet-end process control system to exchange all relevant production and process information of the running order, thus providing a useful analytical database and record of all defects created, cross referenced against this data.
Thanks to its integration with Pro/Syncro, Pro/Quality automatically tracks and ejects any detected waste sheets from the corrugator at the waste diverter located immediately after the cut-off knife. In this way, only sellable boards are passed on to the stacker. Pro/Quality also provides instant operator diagnostics and immediately adjusts relevant machine parameters and process settings to correct the detected defect.
Pro/Quality not only optimises board quality and reduces waste but it also guarantees no defective board from the corrugator is delivered to the plant’s customer.
SOUND BOOTH

- Intro
- Gallery
Fosber has developed a bespoke Sound Enclosure for the complete corrugator line with a totally new streamlined modern design. This unparalleled aesthetic designs results in a truly unique 21st century contemporary appearance for the corrugator that will enormously impress any visitor who enters the production hall area.
The new Sound Enclosure limits sound emissions to below 85 db and conforms to all the latest CE regulations. It means that a corrugator can be installed in a residential area without any problems or limitations to times when the corrugator can be run. The Sound Enclosure has been design engineered using a combination of large areas of "armoured" glass as well as sound-proofed panelling to not only reduce the sound levels but also ensure optimum operator visibility to all the various machine operating areas is retained (which other traditional sound booth designs do not take into consideration). All operator controls and screens form an integral part of the design conveniently mounted on external panels for optimum functionality.
Complete with all operator controls a internal lighting and suitable air extraction systems, the Sound Enclosure has been specifically designed and "tailor-made" for the Fosber corrugator, providing easy and unrestricted operator and maintenance access to all areas of the machine whenever required.